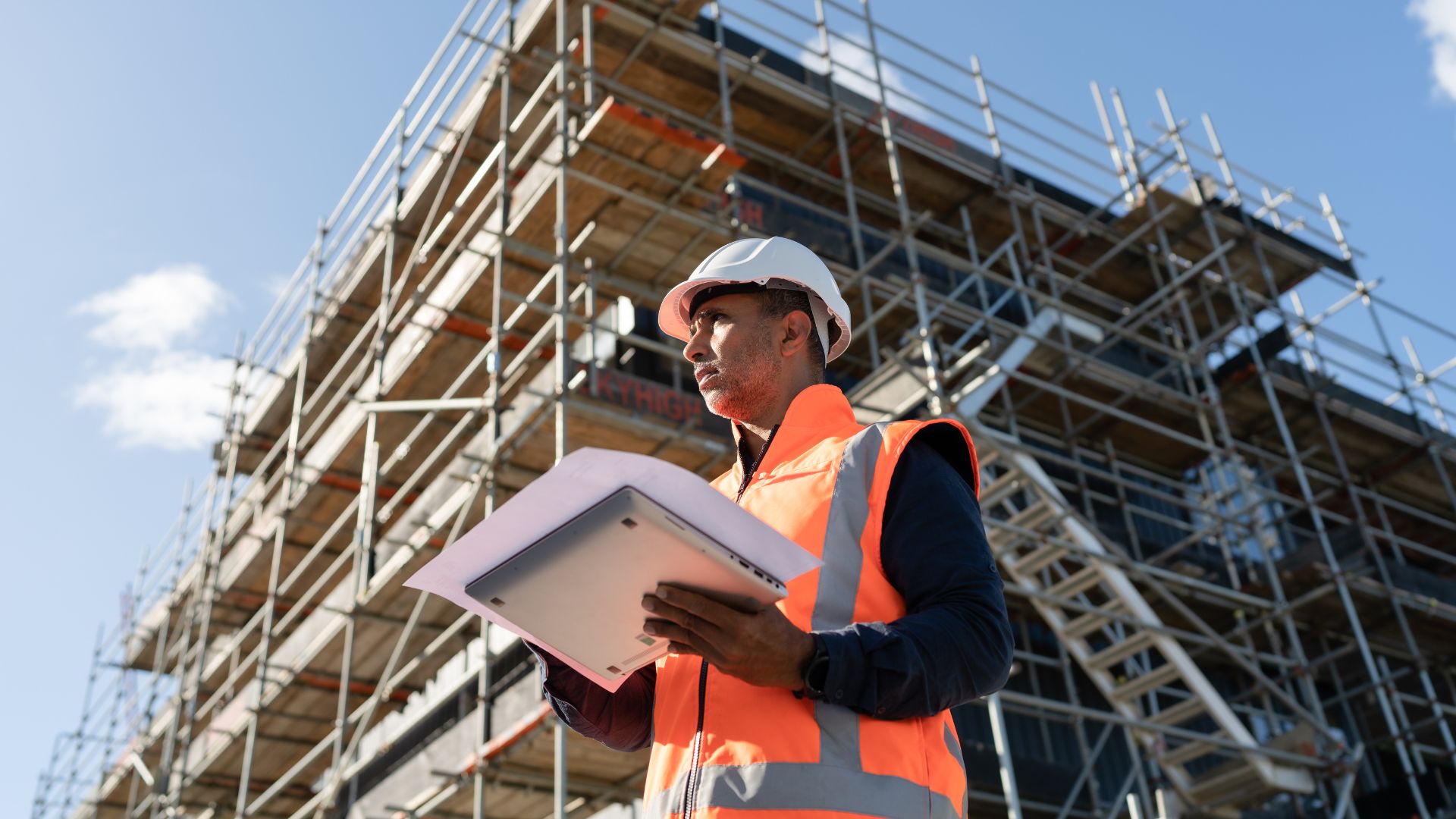
The Hidden Weaknesses in Construction Safety That Negatively Impact Projects
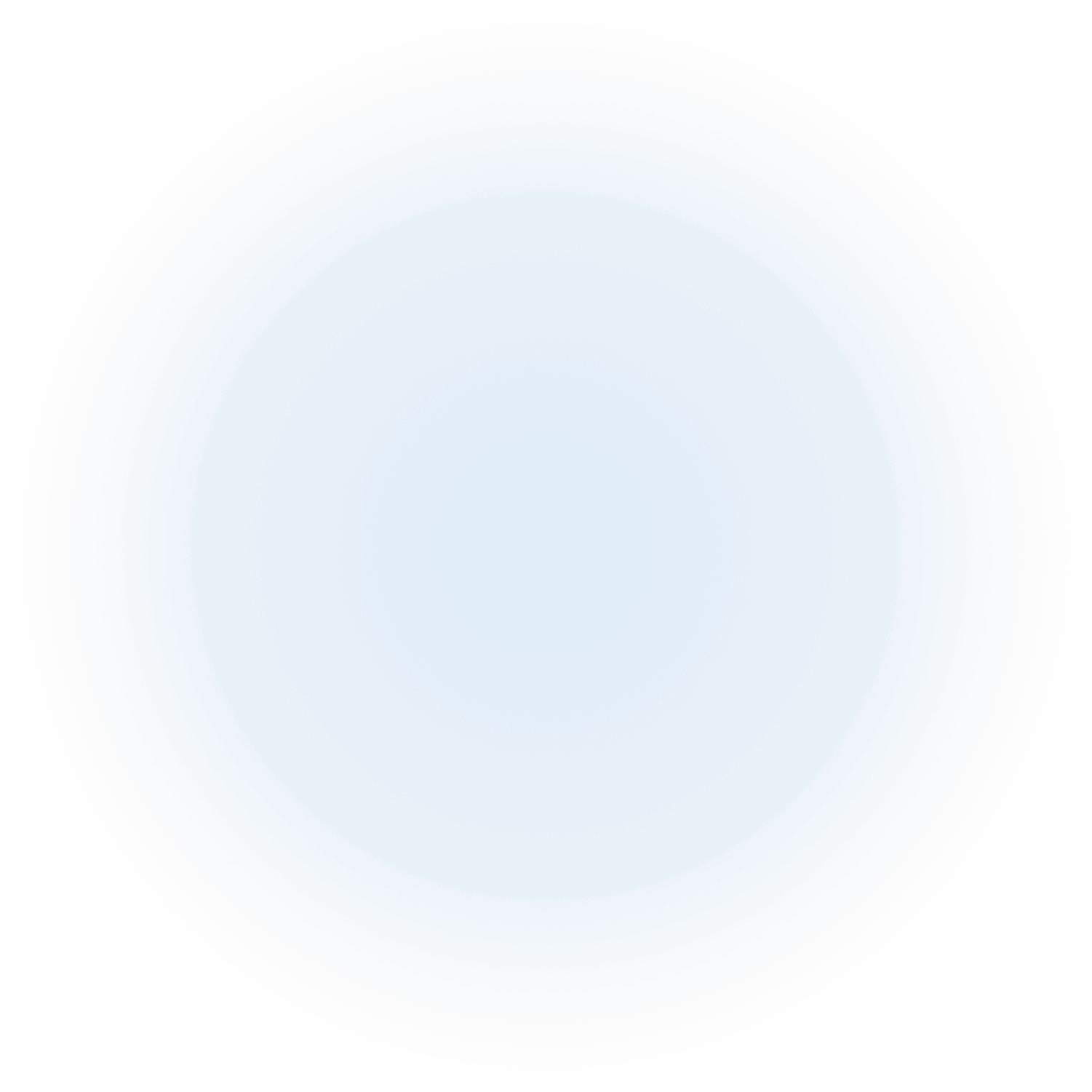
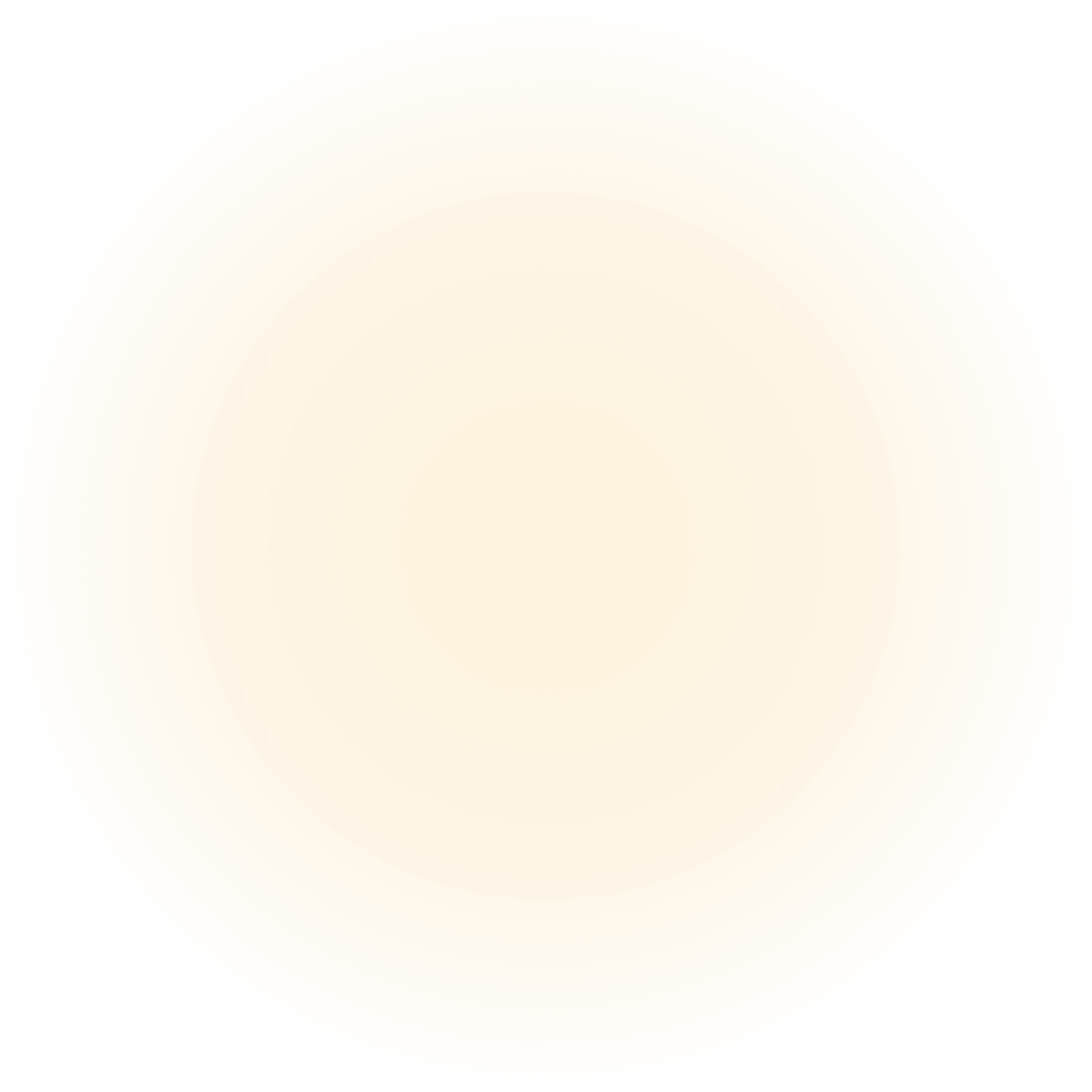
Why More Safety Rules Aren’t the Answer
Construction sites are full of risks from working at heights to heavy machinery, trip hazards, and high-voltage equipment. And while every project implements multiple layers of safety measures to prevent incidents, accidents still happen.
But the problem isn’t a lack of rules, it’s the hidden weaknesses in the system that aren’t visible until it’s too late.
The Swiss Cheese Model explains how incidents occur despite multiple protective barriers. Each layer (policies, training, management oversight) has weaknesses and small “holes” in the defence. A major incident happens when those holes unexpectedly align.
The Swiss Cheese Model: Why Safety Barriers Aren’t Enough
James Reason’s Swiss Cheese Model illustrates that safety failures aren’t usually caused by a single mistake. Instead, multiple small failures combine to create a serious incident. Each layer of safety, whether it’s human behavior, processes, or company culture, has flaws:
- Human Behaviors: Taking shortcuts, ignoring safety barriers, failing to report hazards.
- Processes & Systems: Outdated risk assessments, excessive paperwork, tick-box compliance.
- People & Culture: Fear of speaking up, lack of trust, disengaged workers.
The issue? Most safety programs only focus on plugging one hole at a time. They add more checklists or stricter rules, but they don’t address the underlying causes of risk.
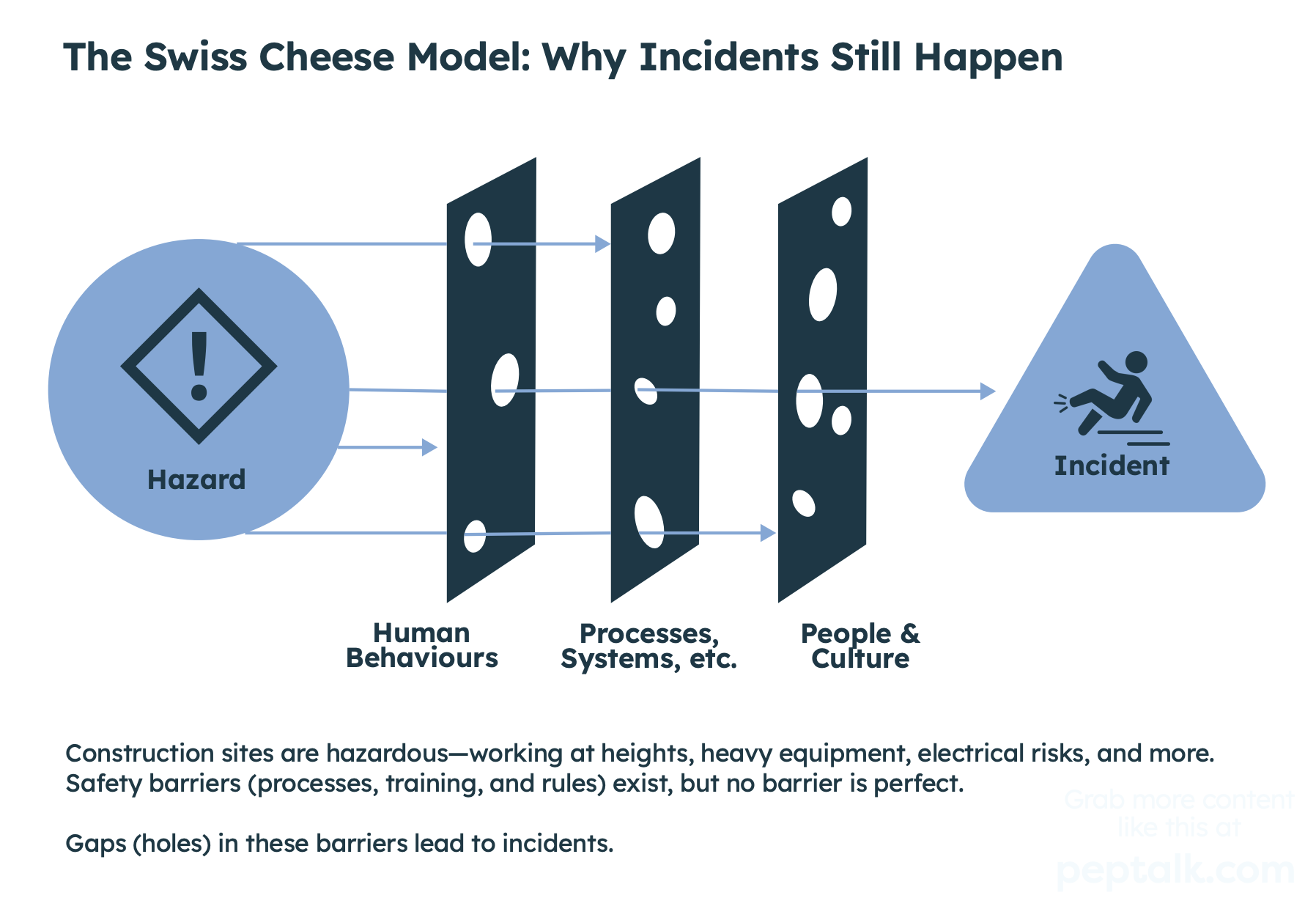
How PepTalk Strengthens Every Layer (Not Just One)
Traditional safety approaches try to fix individual holes while PepTalk ensures each layer is strengthened so the system is resilient, even when failures occur.
Human Behaviors: Making Safety Personal
- Workers take risks when they don’t see why safety matters to them.
- PepTalk’s Check-In and SpotCheck reveal why people cut corners and gives leadership real-time insights into risks on site.
- Instead of enforcing rules, managers can use data and leading indicators to influence behavior.
Processes & Systems: Moving from Paper to People
- If procedures are complex or unrealistic, workers won’t follow them.
- PepTalk gathers direct feedback on whether safety processes and operations are practical so companies can fix inefficiencies before they impact the project.
People & Culture: Giving Workers a Voice
- A culture of fear and blame prevents workers from reporting hazards.
- PepTalk’s anonymous reporting allows teams to speak up without fear, so leadership can address risks before they escalate.
- Safety isn’t about enforcement, it’s about trust. PepTalk builds engagement, communication, and ownership.
Beyond Just Avoiding Incidents: Building a Resilient Safety Culture
The biggest misconception about safety?
That it’s about avoiding incidents. In reality, the safest teams are the most engaged teams.
Research shows that engaged workplaces experience:
✔ 64% fewer safety incidents
✔ 23% higher profitability
✔ 66% increase in worker well-being
(Source: Gallup)
PepTalk doesn’t just reduce accidents, it builds a workforce where safety becomes second nature.
Focus On The System, Not The Symptoms
Traditional safety programs try to patch holes, but the Swiss Cheese Model shows that real safety comes from reinforcing every layer.
PepTalk ensures that safety isn’t just about compliance, it’s about awareness, communication, and action.
Frequently Asked Questions
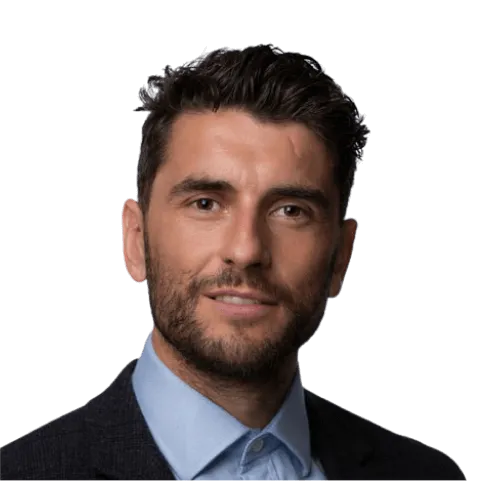

See PepTalk in action
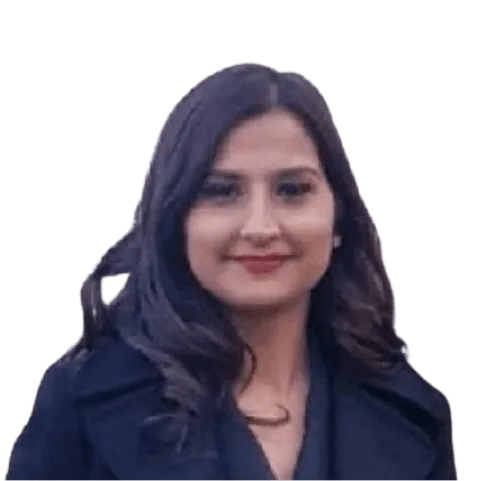
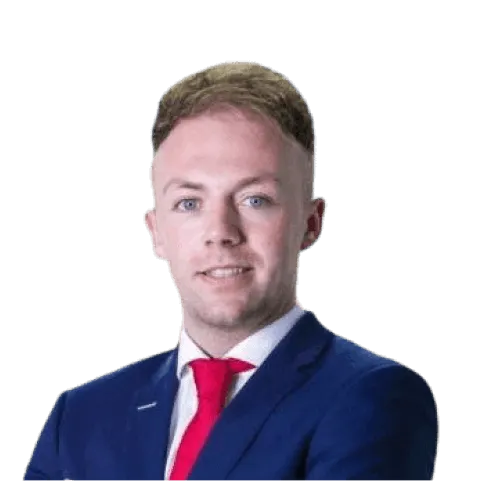
Related
Latest Blogs
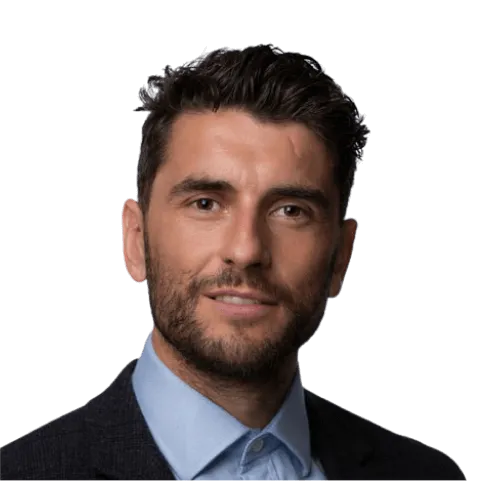

See PepTalk in action
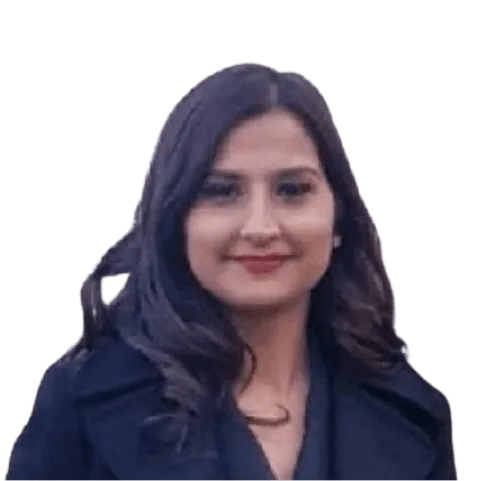
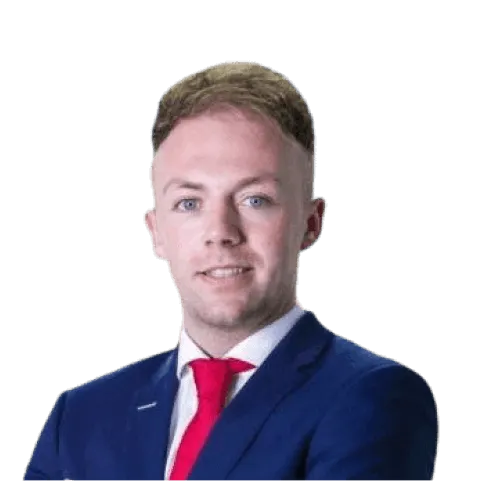